Thermally efficient windows and doors are increasingly important as building codes evolve and energy usage and costs become critical considerations for both commercial and residential projects. When developing the Performance Line, Western Window Systems set out to create a product line that could meet the strictest standards for energy use and meet architects’ needs for sightlines, sizes, strength, and configurability.
Western Window Systems’ Performance Line products adhere to National Fenestration Ratings Council (NFRC) performance testing and rating requirements, meaning the Solar Heat Gain Coefficients and U-Factor values of our products meet energy efficiency standards for resisting solar radiation and keeping heat from escaping a room.
In addition to complying with NFRC and U.S. Department of Energy requirements, Western Window Systems’ Performance Line products also meet California’s stringent Title 24 energy code requirements for both performance and prescriptive compliance paths.
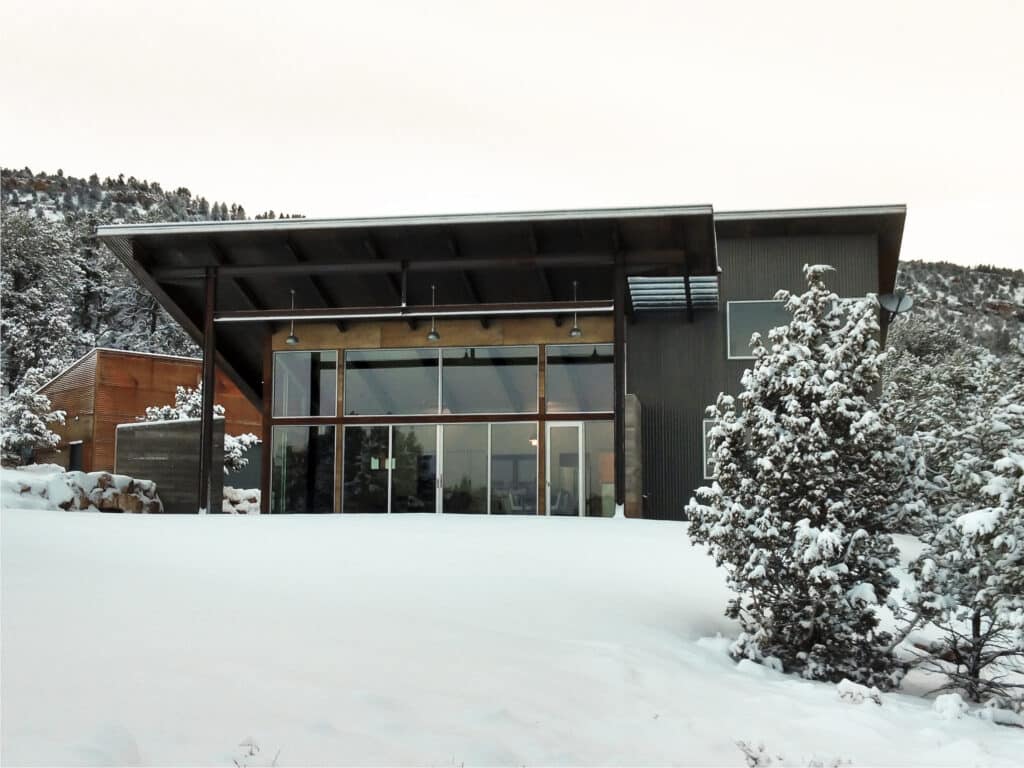
Thermal Performance Factors
Western Window Systems designs our products for thermal performance in several ways. Our Performance Line windows and doors are specifically engineered with the following practices:
- Maximizing low-E, coated, and insulated glass. Low-E, coated, and insulated glass filled with argon gas has a better U-value (thermal transmittance) than what is achievable with just thermally broken aluminum, so maximizing the glass is the easiest thing to do to improve U-value. “Fortunately, maximizing glass is great for energy and reducing the sightlines, which customers prefer,” says Richard Mazur, Western Window Systems’ design engineering manager.
- Filling hollow cavities in thermally broken extrusions. When possible, any hollow cavities within the thermally broken extrusions are either filled with foam or thermal struts with fins, which help break up the hollow space. “The importance of breaking up the hollow space is due to convection,” says Mazur. “When there is a temperature differential between interior and exterior components separated by an air gap, convection currents will be created, causing the air to mix and reduce the air gap’s insulative properties.” Thermal breaks prevent these currents and improve energy efficiency.
- Minimizing thermal bridging caused by hardware components. Hardware, like corner joinery and hinges, usually bridges thermally broken extrusions and cause localized areas with suboptimal efficiency. “In some cases, you might see a spot where frost may form,” Mazur explains. “This can be avoided by using engineering plastics over metal components, or use insulative spacers between the metal components being joined.”
- Ensuring no interior and exterior metal members have separations of less than ¼ in. from each other. This is done to guarantee a truly thermally broken system per NFRC guidelines, even where the requirements of a new product are more relaxed in terms of energy performance.
What to Consider
Three major considerations in the thermal performance design of Western Window Systems’ Performance Line products are structural performance, aesthetics, and thermal expansion.
- Structural Performance. Performance Line doors’ resistance to wind load is boosted by where the thermal break is placed in the extrusion. “Structurally, when you add a thermal break, you are going to be producing a less stiff shape. This is due to the interface between the thermal break and the aluminum,” Mazur says. “For example, on the Performance Line, the crimps that hold the thermal strut in place will break free once a certain transverse shear stress is reached.If this limit is reached under wind load, this will cause the crimps to fail and cause the stile to suffer permanent deflection., even though we did not reach the yield stress limit for the aluminum. We can improve the stiffness/performance by where we place the thermal break in the extrusion.”
- Aesthetics. When Performance Line doors are in a closed position, the thermal break is hidden with an aluminum cover on the interlock style. “For instance, on one Performance product we are developing, we made a cover piece to hide the black thermal breaks,” Mazur says. “In the interlocker design on the Series 7600, no thermal break is seen when the door is closed.”
- Thermal Expansion. As thermal performance improves on a product, problems with thermal expansions can arise. “For example, when the sun is low in the sky in the fall and it’s shining directly onto our multi-slide door that’s anodized bronze, the exterior extrusion could reach up to 200 degrees Fahrenheit, while the interior maintains a temperature close to whatever the air conditioner is set to,” Mazur says. “Due to thermal expansion, this means that for a 96-inch tall door, that hot stile has grown over 1/8th of an inch. The strain induced by that growth causes the stile to bend.” One solution employed in some cases, including in the Series 7600 lead stile, is a sheer-free strut, which allows the two extrusions to slide past each other.
Testing, Testing
Western Window Systems’ Performance Line doors and windows aren’t just built for thermal performance – they’re also tested for it in three phases:
- Developmental Phase: When developing our products and testing their thermal performance values, Western Window Systems utilizes the standard 2D computational fluid dynamics (CFD) software, Therm, that is used by the fenestration industry in the United States for analyzing the thermal performance of windows and doors.
- Physical Tests In-House: Western Window Systems performs physical tests on initial prototypes for air infiltration and exfiltration to ensure that the seals specified for the design are adequate in real-world testing.
- Third-Party Testing: To get certification for the simulated values in the developmental phase, a third-party testing facility must both perform the CFD analysis themselves and test a physical specimen in a special test chamber. The physical specimen must come within 10 percent of the calculated performance values to pass.
The Performance Line is designed, tested, and proven to achieve goals for energy efficiency without sacrificing design – and in some cases allow for greater design capabilities by allowing taller and wider sizes.